At a high level, Generative design is relatively simple. It is a capability of CAD generative engineering applications that autonomously generates a number of design alternatives given a set number of constraints. This can be done without an engineer’s guidance or interaction, freeing them up for other tasks. Once complete, the engineers can choose which designs they want to explore more completely. In all, this accelerates the design process without detailed attention from the engineer.
Generative design in computer-aided design (CAD) is an innovative approach that involves using algorithms and artificial intelligence (AI) to generate multiple design options based on specified parameters and constraints. It allows designers and engineers to explore a wide range of potential solutions and optimize designs for various objectives such as weight reduction, material efficiency, cost minimization and performance enhancement. Generative design in CAD is particularly valuable for complex engineering challenges where traditional design methods may be limited by time, resources or human creativity. By leveraging computational power and generative engineering algorithms, generative design empowers designers to create optimized, innovative solutions that push the boundaries of what is possible in product design and engineering.
Key characteristics of generative engineering in CAD
Algorithmic optimization in generative design:
Generative design algorithms analyze input parameters such as functional requirements, material properties, manufacturing constraints and performance criteria to generate design solutions.
Iterative exploration in generative design:
Designers can explore numerous design alternatives quickly and efficiently. Generative design tools typically generate a multitude of design options, which can then be evaluated based on specific criteria.
Complex geometry in generative design:
Generative design often produces complex geometric shapes and structures that may be difficult to conceive manually. These designs can leverage the full potential of advanced manufacturing techniques such as additive manufacturing (3D printing).
Multi-disciplinary optimization in generative design:
Generative design can optimize designs across multiple disciplines, such as structural analysis, fluid dynamics, thermal management and electromagnetic simulations, to achieve optimal performance across various criteria.
Human-in-the-loop in generative design:
While generative design algorithms automate the creation of design alternatives, human designers play a crucial role in specifying design requirements, evaluating generated options and refining the final design.
Exploration of design space in generative design:
Generative design allows designers to explore the entire design space, uncovering innovative solutions that may not have been considered through traditional design methods.
Parametric modeling in generative design:
Generative design often utilizes parametric modeling techniques, where design parameters are defined and manipulated to drive the generation of design alternatives.
Generative design and topology optimization
Generative design supports key capabilities like topology optimization for performing structural simulation and removing load-weight from empty area in materials. Siemens NX 12 is the only generative design software that embeds topology optimization powered by convergent modeling technology which enables unified 3D modeling capability on combinations of Facet and B-rep data. This results in lighter components without sacrificing design intent or integrity.
Empowering engineers with generative design and facet modeling
Generative design is a CAD engineering software function in which a designer collaborates with artificial intelligence algorithms to generate and evaluate hundreds of potential designs for a product idea. The generative design process starts with defining the goals and constraints of the project. These include, but are not limited to, design parameters such as:
- product size or geometric dimensions
- permissible loads and operating conditions
- target weight
- materials
- manufacturing methods
- cost per unit
Related products: NX CAD
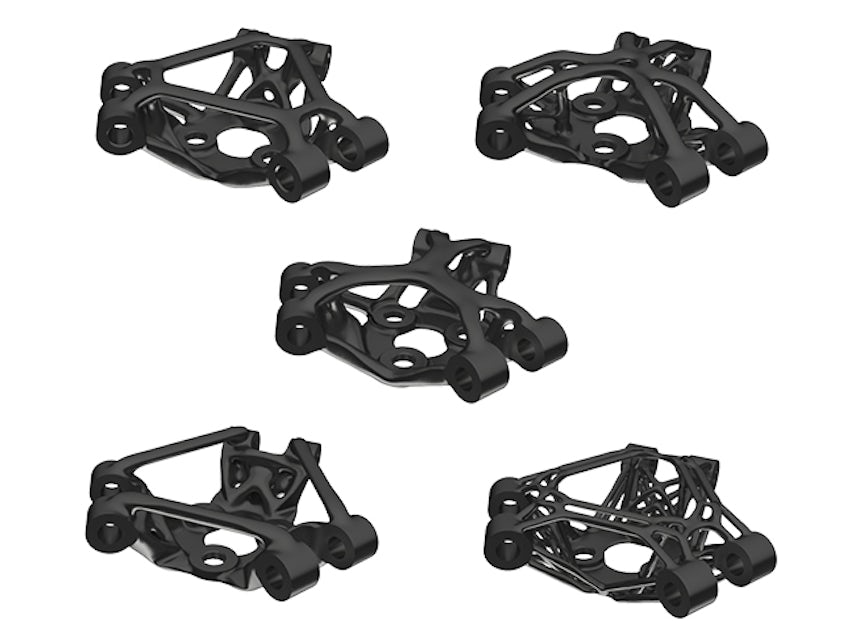