Companies today are facing growing pressure to bring better products to market faster and at a lower cost. Getting performance attributes, such as noise, vibration and harshness, comfort, durability, and multi-attribute balancing right is more complex and important than ever before.
Simcenter Engineering and Consulting Services partners with you to determine the right simulation process and tools to help you overcome these challenges without compromising performance. We also work with your engineering teams to benchmark current simulation challenges and develop a roadmap to achieve digitalization maturity.
Related resources
Blog: Making your historical NVH data work for you
Case study: Hyundai Motor Group uses AI to reduce subsystem parameter optimization from one week to 15 minutes
Case study: Hyundai leverages Simcenter Engineering and software to balance handling, NVH and ride comfort
Case study: Ford Otosan leverages accelerated durability testing cycles to cut weight and costs
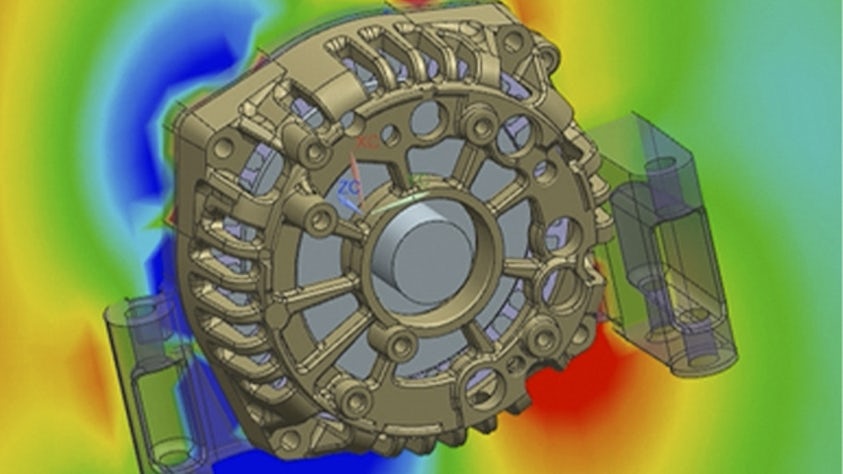